Umair,
This is the actual process for the manufacture of this item:
- Cut steel bar (in shop)
- CNC lathe (in shop)
- Detail (in shop)
- Mark (in shop)
- Heat treatment (external supplier – it’s a service subcontracted
I tried three different ways and in all cases I’m using Production Planning Tool:
Number 1.
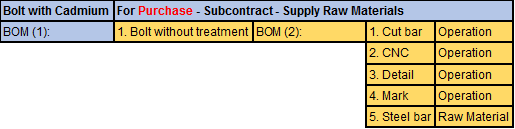
This way, the Production Planning Tool creates a Production Order for “Bolt without treatment”, then, from there it’s created one Material Request – Manufacture for “Bolt without treatment”, and may create a Material Request – Purchase for “Steel bar” if there´s no inventory.
The Material Request – Manufacture for “Bolt without treatment” has no effect, already exist a Production Order. So, ERPNext allows to finish the Production Order, and no Purchase Order was created to supply subcontracted service for “Cadmium Treatment”.
I know the manual and videos shows that from the Sales Order must be created a Material Request – Purchase, but the job of Production or Manufacturer Manager is to pull the Sales Order and program manufacture in shop and program subcontracted services, to the Sales Person.
Number 2.
This way, the Production Planning Tool creates a Production Order for “Bolt with Cadmium”, then it’s created one Material Request – Purchase for “Cadmium Treatment”, and may create a Material Request – Purchase for “Steel bar” if there´s no inventory.
Start the Production Order, then it’s created a Stock Entry to transfer the Steel Bar, and then ERPNext allow to finish the Production Order without making the Purchase Order for “Cadmium Treatment”. That’s because the Stock Entry from Manufacture automatically and only includes materials from Raw Material Warehouse.
Number 3.
This way, first I changed the source warehouse for the subcontracted service, then Production Planning Tool creates a Production Order for “Bolt with Cadmium”, then are created two Material Request: one to Purchase “Cadmium Treatment” and a second for Manufacture “Bolt without treatment”, and of course it may create a Material Request – Purchase for “Steel bar” if there´s no inventory.
Start the Production Order and it’s created one single Stock Entry-Material Transfer for “Steel bar” and “Heat treatment” …I can’t do an entry stock for a subcontracted service that hasn’t been made before the bolt is manufactured, the Production Order can’t be started this way. So I just erase the “Heat treatment” from this first Stock Entry–Material Transfer.
Back to the Production Order, now is In Process, click on Finish, and it creates a Stock Entry that lists:

Obviously ERPNext doesn’t allow to submit this Stock Entry because there’s no receipt for the Cadmium Treatment, so again I just erased it and Submit. Then the Production Order indicates Completed. Once again ERPNext allow to finish the Production Order without making the Purchase Order for “Cadmium Treatment”.
At this point I was hoping that the Production Order as a further step, request a Stock Entry for the “Heat Treatment”, so this takes me to two possible solutions:
From the step before, I’ll have to make sure that the Production Manager never find that the “Heat Treatment” can be also erased to do the Stock Entry from Manufacture and finish the Production Order, and so be obliged to complete the Purchase Order for the “Heat Treatment”. (This issue can’t be solved just modifying some permissions, because at the first Stock Entry – Transfer Material it’s necessary to erase the subcontracted service).
Or…
Number 4.
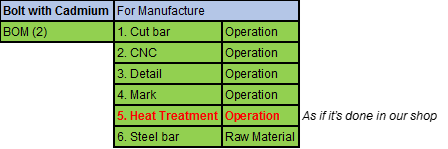
This way, the Production Planning Tool creates a Production Order for “Bolt with Cadmium”, it’s created a Timesheet and a Stock Entry for the “Steel Bar”. Back to the Production Order, now is in Process; complete and Submit the Timesheet, then can be finished the Production Order.
But this way I have to create an unliked Purchase Order to the Production Order, for the “Heat treatment” (subcontracted service) and depend completely from one person to do this parallel process before the Production Order is finished.
I just can figure another way to structure these BOMs so ERPNext requires the purchase for the subcontracted services, every step with no exceptions and in the right order. I know ERPNext team is in process to improve the manufacture module, so I hope my situation contributes to do so.
¿Or is there any other way to do it?
By the way, I’m also posting here our conversation, it may be helpful to others or maybe someone else had figured another way to solve this.
Regards.