So, with the release of nested warehousing (thank you!) I’m trying to figure out how best to use it to meet my needs. So, I thought I would start this thread to allow for another discussion on this. So, Here’s a breakdown on how I am gathering that this works:
-
There is a parent warehouse, called ‘Warehouses’. This contains all of the warehouses in the system, including warehouses in multiple companies. This ‘group’ warehouse cannot be used in transactions.
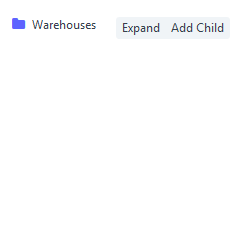
-
When expanded, the ‘child’ warehouses can be either ‘group’ or ‘non-group’ warehouse types. ‘group’ type warehouses cannot be used in transactions, but ‘non-group’ ones can.
So, the problems that I’m facing is that I have attempted to setup our stockroom as a nested set:
- Stock Room - MC
- Aisle D1 - MC
- Shelf A - MC
- D1A1 - MC
- D1A2 - MC
- D1A3 - MC
- Shelf B - MC
- D1B1 - MC
- D1B2 - MC
- D1B3 - MC
This works beautifully as an organizational tool, however when it comes to using these in practice, there are a few problems.
When attempting a Stock Entry for transfer, the warehouse list is not organized by this method, it’s just random:
I feel like this should be organized by the same structure.
When selecting the source warehouse for an item, the filter list should only show warehouses that the have inventory of the selected item.
The warehouse should show the available quantity of the item, just like the available quantity of batches is shown when selecting.
If anyone else has any suggestions for improving the warehousing in the system, or has any problems, please post in this thread.
3 Likes
This is an interesting idea - and probably could be implemented easily with a custom script / field (if you wanted to test it out). I’m curious though: What happens if you don’t have any stock?
I think a better solution might be to just set the default warehouse of the item and have that auto-populate. No?
1 Like
Well, If you don’t have any stock, then you wouldn’t be able to use ‘Source Warehouse’ anyways, right?
And, I’m not sure about general usage, but in our company’s stockroom, there are no fixed locations. Goods could be in location D1A3 today, but D7J2 next week. Granted, this could be reduced somewhat…
1 Like
Another problem I am having is automatic reorder levels. It should be possible to select a parent warehouse and have the total calculated from that.
@cpurbaugh are you currently using a “Slotting System” for inventory management?
We are interested in this topic as we will be implementing a custom ERPN system for a new client in a few months and they want to enable a slotting and dynamic slotting system.
You mentioned the inventory could reside anywhere from one week to the next in the warehouse.
For context, here is a basic overview of slotting in WMS
@Eric_Delisle No, our company doesn’t use a slotting system. The reason for the frequent moves of stock is making space. our stock room is filled almost to capacity, so things get moved around alot to make space.
As far as setting up a slotting system, I’m not sure how you could make ERPNext do this without extensive development.
Thanks.
That is what we do… “Extensive Development” to help companies realize what they “wish” a system could do. 